The Challenge
A global beverage company needed to ensure the safety of their workers across a variety of unique production lines without interrupting their operations. Their main concern was preventing falls into conveyor systems, but safeguarding these lines proved complex due to several factors:
- Unique Lines: Each manufacturing line is unique and overseen by several departments (Safety, Maintenance, Production), each with their own unique concerns and needs.
- Minimal Disruption: Installation had to occur without impacting production speed. Shutting down lines for extended periods was unacceptable.
- Flexibility for Approval: The chosen solution needed to accommodate on-the-fly modifications to address individual departmental concerns.
The Solution
SpaceGuard’s RageWire® Machine Guarding system, combined with BeastWire® Swing Doors, offered the perfect blend of security and flexibility. Here’s how it addressed the challenges:
- Pre-planning and Department Input: SpaceGuard collaborated with the client’s safety department to define general guarding areas and assemble a parts list. Each guarded area was packaged separately for easy identification and distribution.
- On-Site Customization: The installer laid out the modular RageWire® panels and posts for on-site review by each department. Modifications like cutouts and adjustments were readily made, ensuring everyone’s needs were met.
- Zero Downtime Installation: The modular design facilitated quick adjustments without shutting down production lines.
Client Testimonial
“The ease of field modification with RageWire® was crucial. We could address each department’s concerns and complete the installation without impacting production schedules.” – Kevin Rush, National Material Handling
The Results
The RageWire® system successfully addressed the long-standing safety concerns while fostering collaboration amongst various departments. The modular design allowed for on-the-fly adjustments, ensuring everyone’s needs were met, and the project was completed efficiently.
- Enhanced Safety: The guarding system eliminated the risk of falls into conveyor systems, prioritizing worker well-being.
- Departmental Satisfaction: Collaborative planning and on-site adjustments ensured all departments were involved and their needs addressed.
- Maintained Production Efficiency: The modular design facilitated a smooth installation process with minimal disruption to production schedules.
Project Details
- Dealer: National Material Handling
- Customer: An international beverage maker
- Products: RageWire® Machine Guarding and BeastWire® Doors
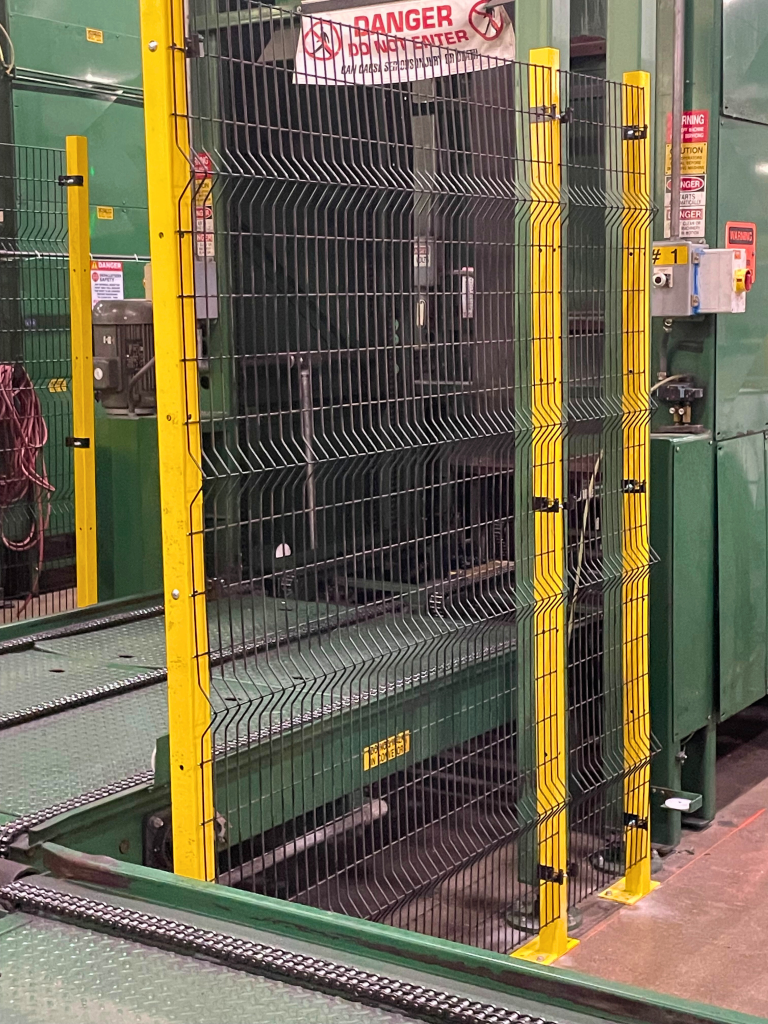
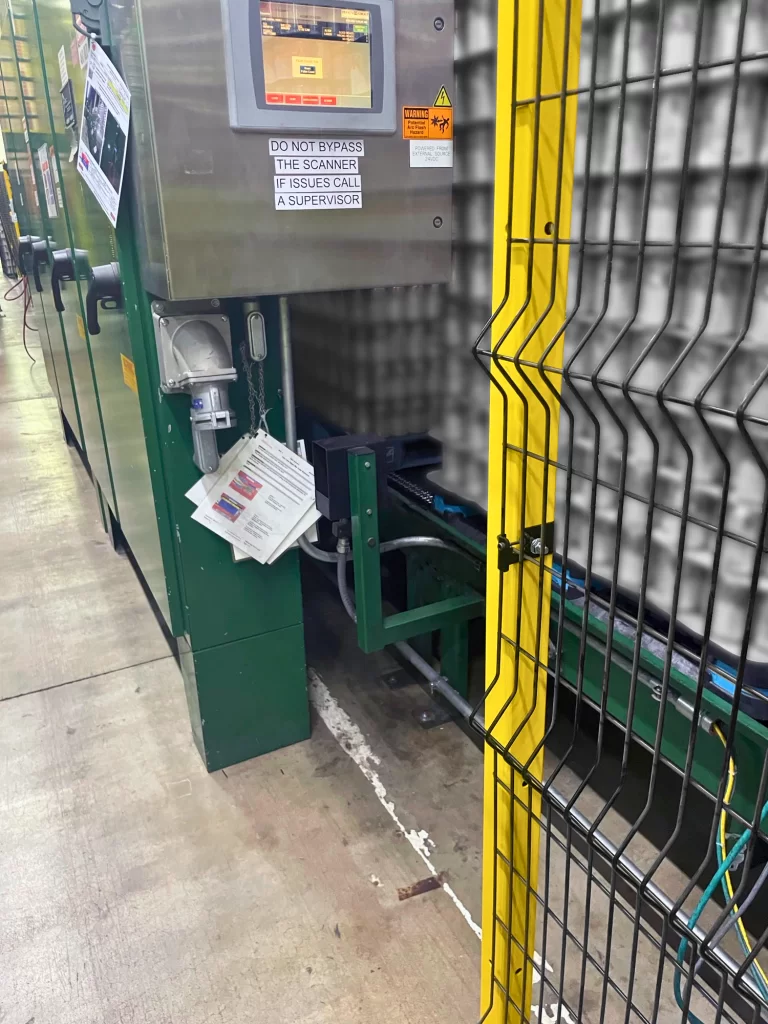
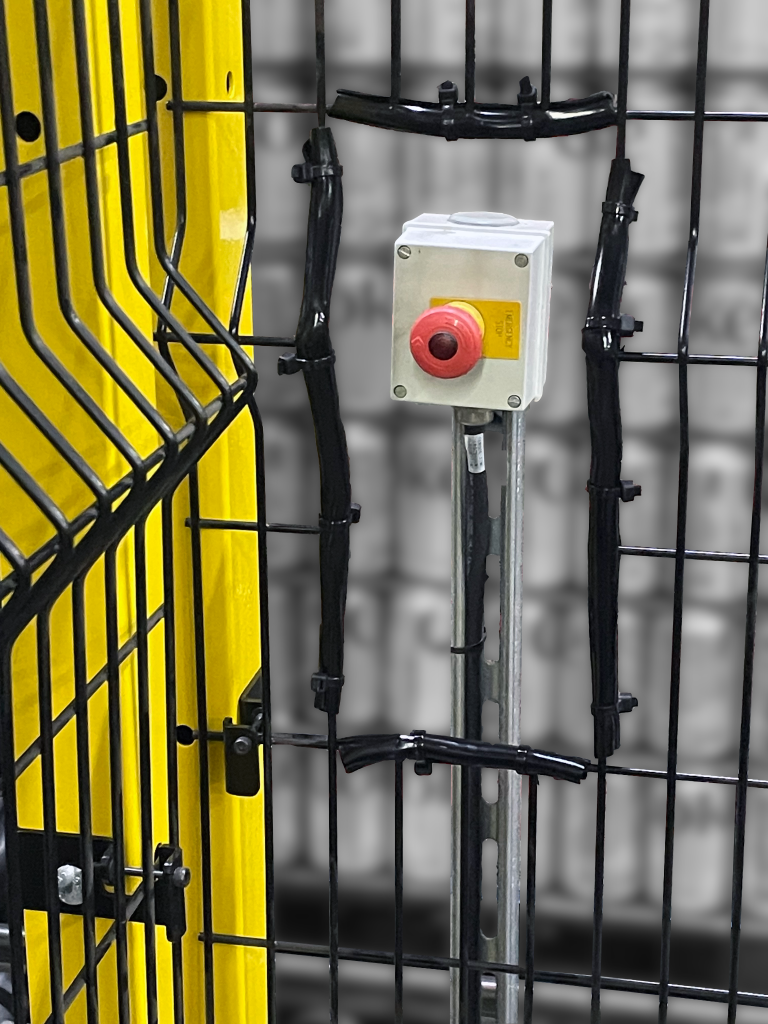
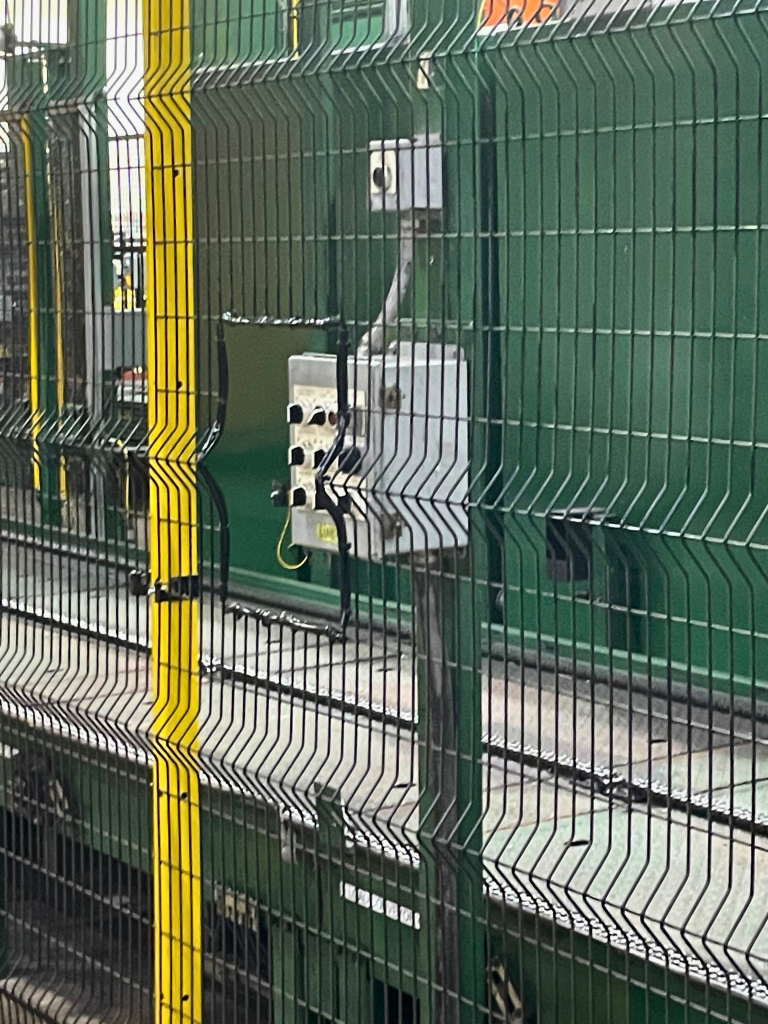
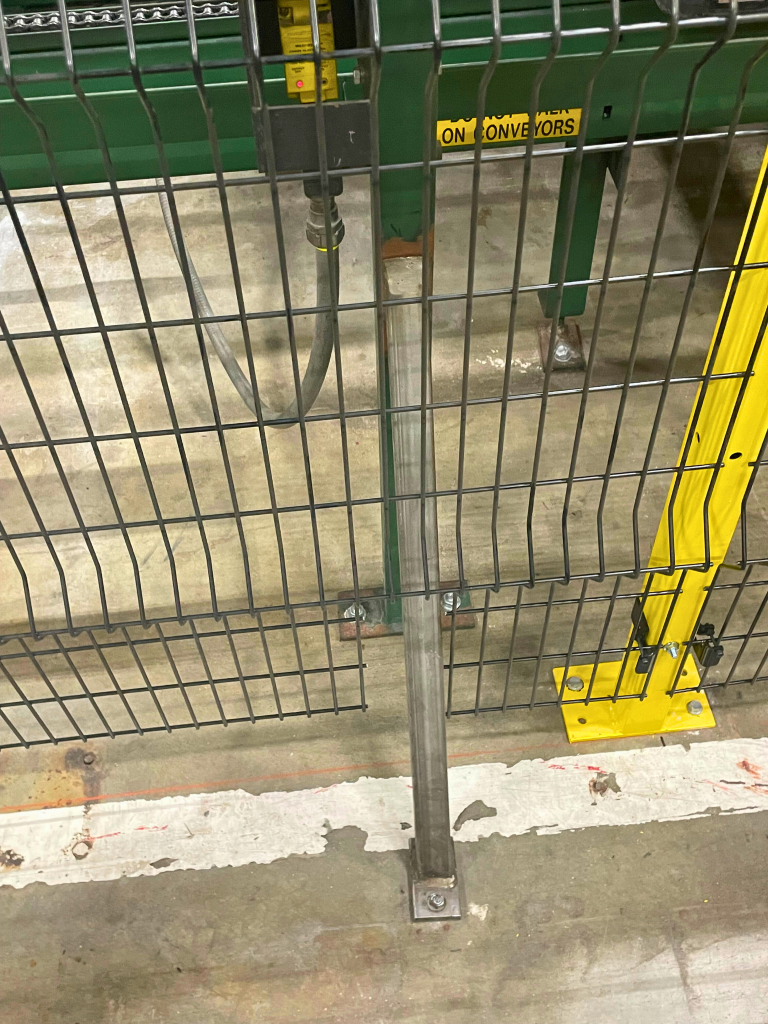